Rising from the Ashes
Part 1
By Andrew Row.
Thought it was time to do a follow up after the fire article a few months back. It’s hard to believe it is only two months since the donor bike arrived, and the rebuild began in earnest.
Feels like years of work as I write this with matchsticks propping my eyes open. The donor bike seems to have been a good gamble from the online auction. Was certainly someone’s pride and joy before it took a slide down the bitumen. We have such a wasteful society when you think an 8000km old rideable scratched bike is a write-off, never to be registered again. Felt a bit criminal to wreck it for parts.
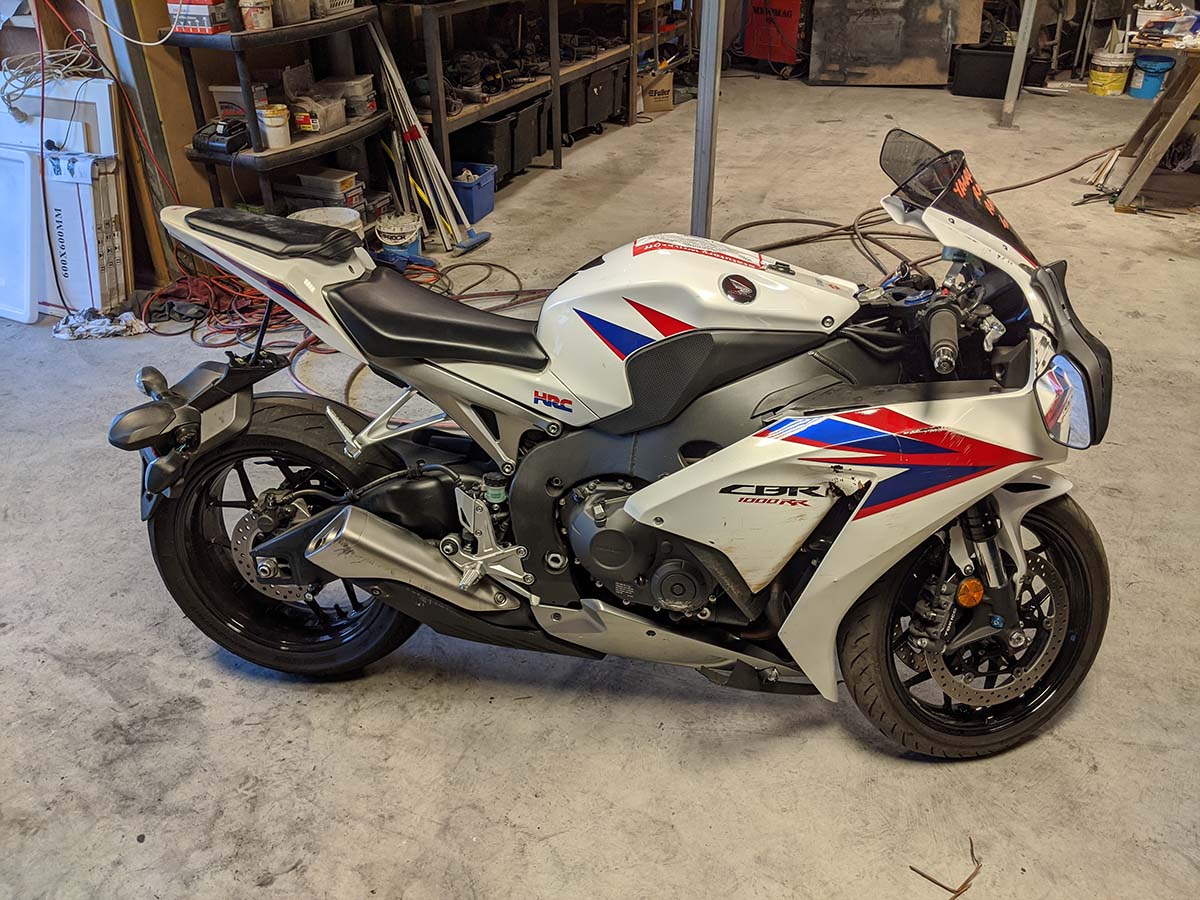
Having loaded the majority of the car into the trailer to be dumped, there was a never ending list of parts to be ordered. Was like Christmas with parcels arriving daily. The local postie and couriers got so familiar they happily wandered through the office to drop things on my desk at work.
Assessing the burnt mess revealed that the fire was hot enough to melt aluminium in places, but not hot enough to melt copper. This should mean no concern for normal steel components, but anything high tensile or heat treated had to go. The three page bolt list kept the man at the bolt shop busy for an hour to pick and pack them all. Being all Ford Sierra bits led to an order from the UK for all the ball joints, tie rod ends, bearings etc after just receiving blank looks from the local parts guys when mentioning Ford Sierra. Cheaper from the UK anyway, along with steering wheel, harness, master cylinders etc all at half what they could be bought for here.
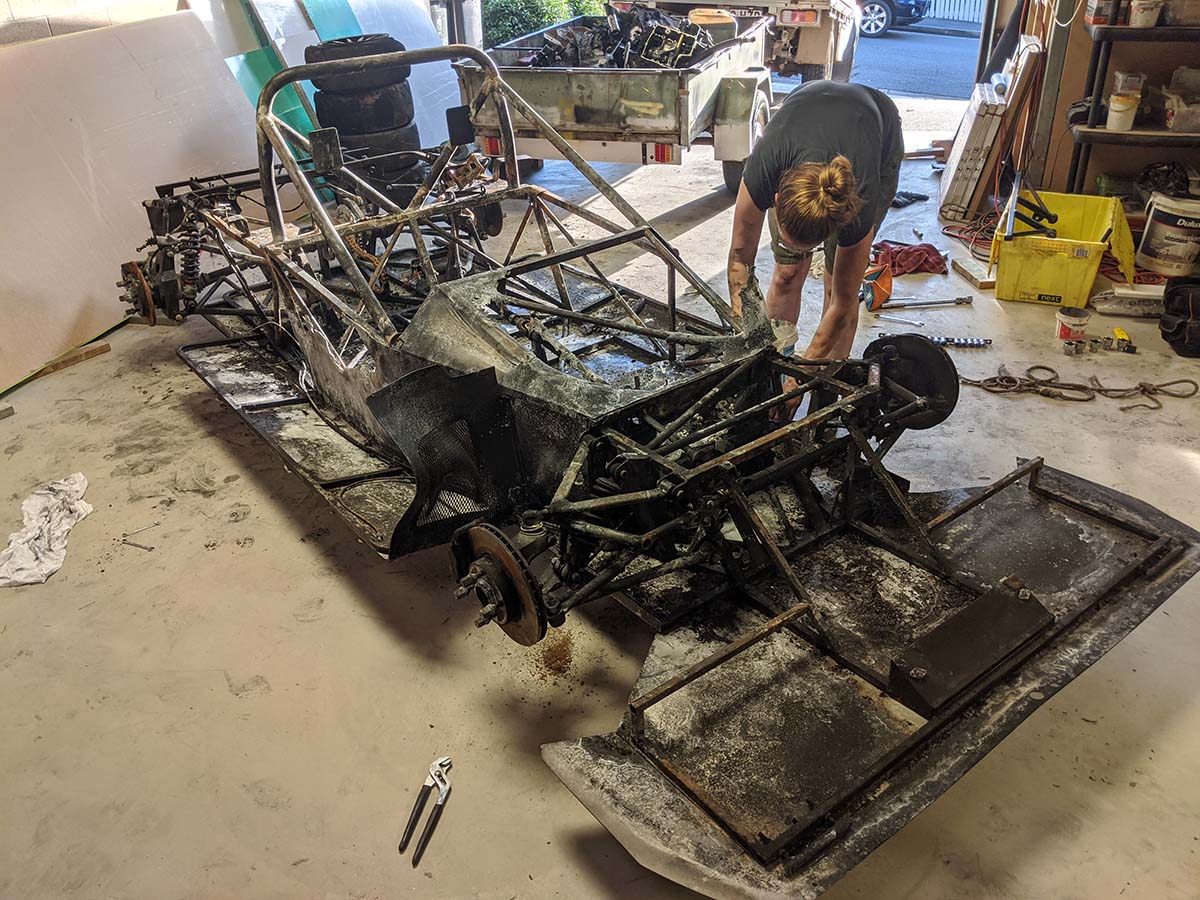
Stripping every part of the suspension and driveline is a long and demoralising task when it’s all burnt and corroded. Fire extinguisher powder is amazingly corrosive. Fortunately Bride is a wiz with degreaser and steel wool, and could return nasty looking parts looking like new as quickly as I could strip them. Got through a few wire brushes on the grinder as well. Bit of team work to keep moral up. Surprising some of the parts that were salvageable. The engine bay floor and diffuser was fine with a good clean, well after we straightened out the bent fins after yours truly spun it trying to go full throttle under the bridge the run before. Apparently that isn’t possible without the rear wing, but that’s another story.
The bright side of the rebuild is the chance to upgrade things that were never great. Car had a Sierra steering rack that was far from ideal length and gave absurd bump steer. Although the old rack was 2.8 turns lock to lock, it always seemed slow to steer. After the fire burnt the boots off it revealed that someone made it a “quick” rack by putting lock stops on it to get the right turns lock to lock. The brand new 2.4 Escort rack will make a massive improvement to steering response, steering lock, and bump steer.

The idea of buying the complete doner bike was to steal as many parts as possible and remove the need for custom tunes etc – being a budget track toy. The bike runs a self-regulating fuel pump with no return lines etc. So to allow the bike pump to be kept a custom fuel tank was knocked up from steel sheet in the workshop after silly prices and lead times were received for farming the job out.
All the exhaust headers and airbox were kept so the tune would be good. The airbox is huge and tall, but it contains four of the eight fuel injectors, so was easier to build the body around it than work out how to revise it. It took a lot of hours staring at the wiring diagram before I took the leap of faith to cut out all the unused sections and override all the tip sensors and side stand switches etc. Turns out only cut one wire too many. The instrument illumination wire from the light circuit actually turns the dash on, not just the back lighting. Quick fix and it fired up and so sweetly.

Have made good friends with our local waterjet cutter, with all manner of parts being cut and folded as required. Fortunately still had a bunch of the aluminium chassis panel cut files from the first build, so they were easy wins.
Bike engines aren’t normally built for cornering forces in the oil pickup. A quick google of what the pommy lads use for sump baffle plates on a Fireblade, along with some tracing paper and a scan on the work photocopier soon had a cut file for a baffle plate.

Next challenge was a lack of available front sprocket sizes, so a custom rear chain sprocket was drawn up from a long list of formulas, with tiny arcs and tangent lines that are all a bit irrelevant when drawn out to scale, but should do the job for the revised gearing on the new motor with its 13000 rpm redline. The aluminium body sidepods and radiator ducting were a challenge to my level of 3D drafting skills, but all fitted nicely with the idea of having a bit more side impact protection than the previous glass panels.
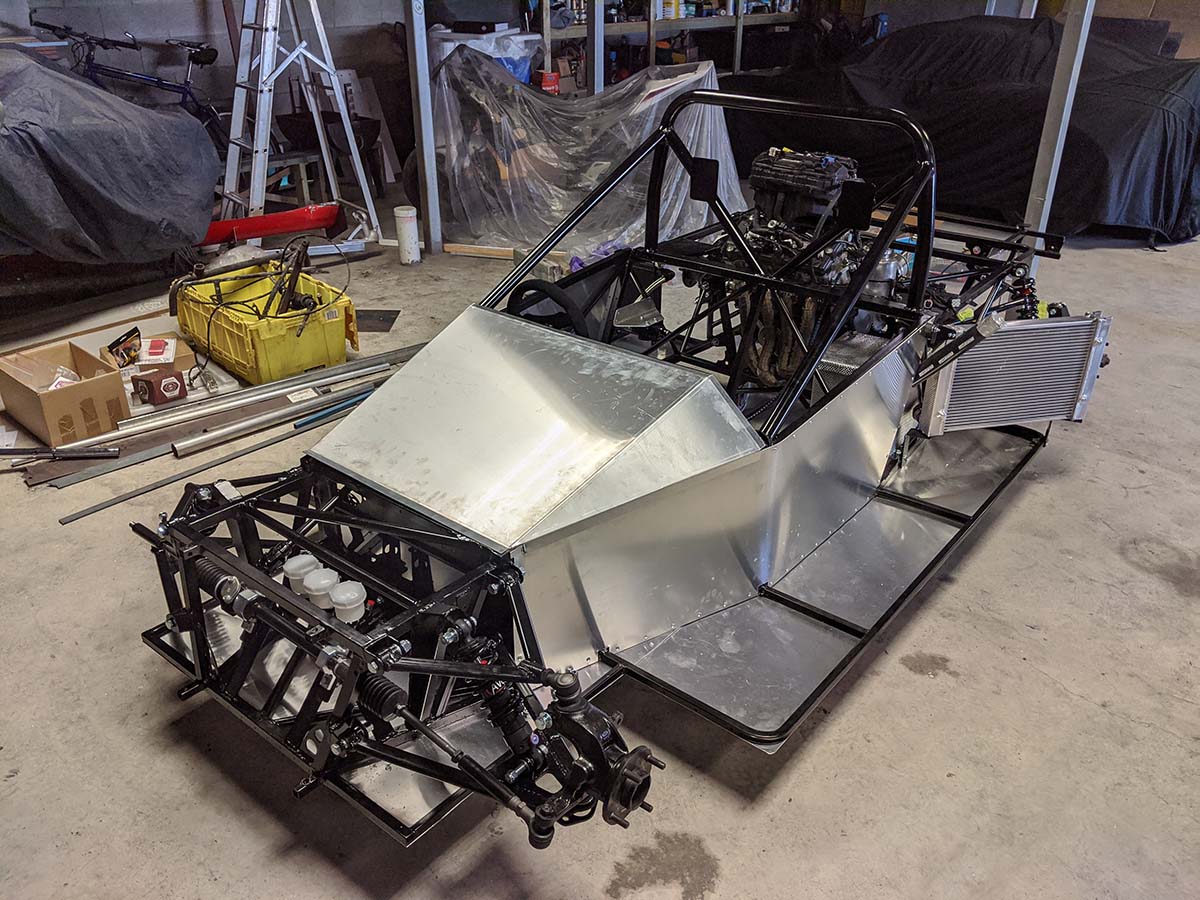
Speaking of panels, it has been the most asked question. Where will you get a new body from? To which I casually replied I would make one. Receiving the quizzical looks that one would expect, but we pressed on with the plan none the less. A couple of weekends and a bunch of mdf has made the beginnings of some one off molds. Have avoided the temptation to go down the road of full blown plugs and glass molds as it just doesn’t seem worth the time. Should get panels from these that are at least as good as the previous set. Will keep you posted in Part 2 how that turns out.
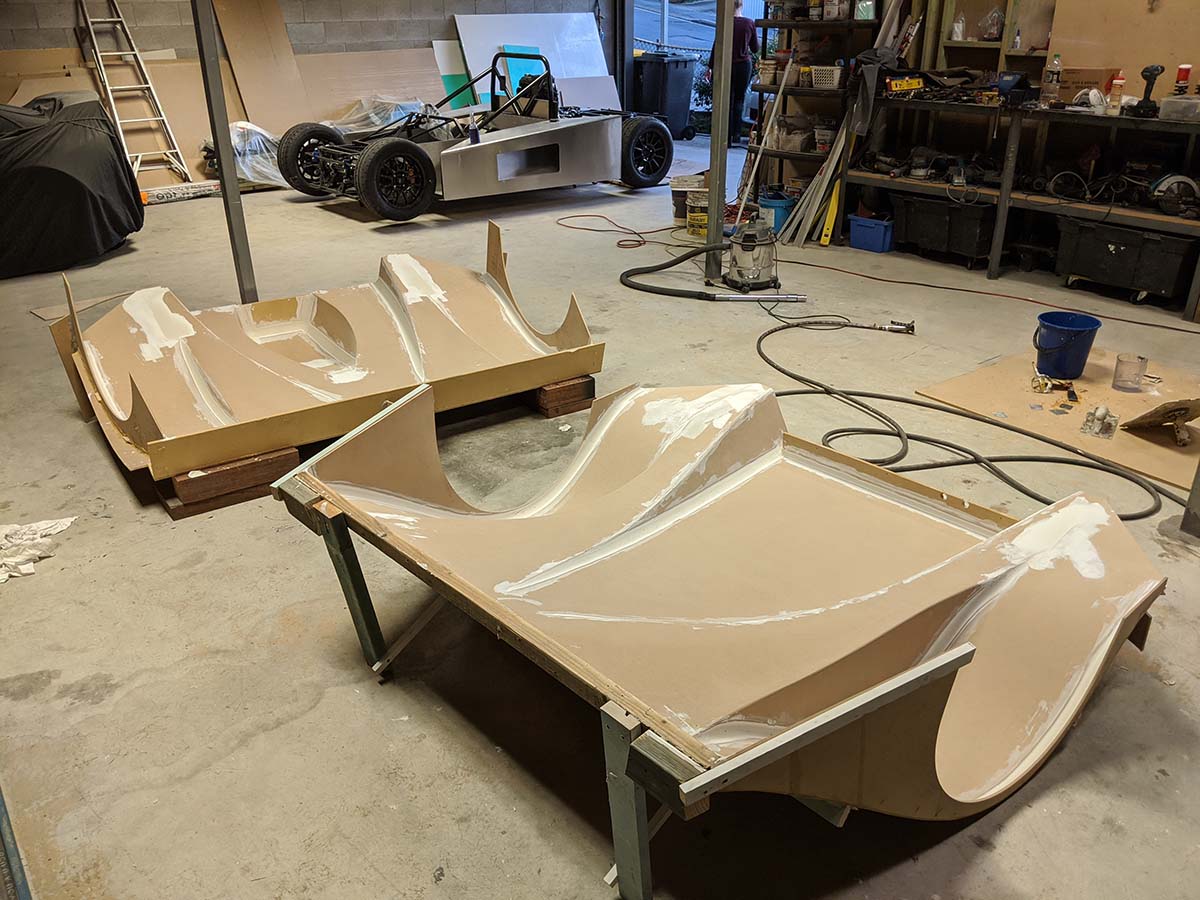

Off to the DTC this weekend as an open wheeler for a test run. Then a month to get a body on for Morgan Park. All easy if we just avoid sleeping.